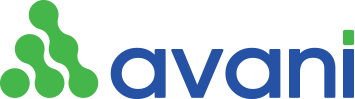
What is Automated Machine Maintenance Monitoring? Benefits and Practical Applications
Benefits of Automated Machine Maintenance Monitoring
The monitoring system helps detect early signs of damage, thereby minimizing unplanned machine downtime and optimizing production efficiency.
By performing maintenance based on real-time data, businesses only need to repair when necessary, avoiding wasting resources and unnecessary parts replacement costs.
Continuous monitoring helps machines to be properly and promptly maintained, increasing the durability and life of equipment.
Monitoring systems provide detailed information about machine performance, from which businesses can optimize production processes.
Automatic maintenance monitoring helps detect potential risks in a timely manner, protecting the safety of employees and business assets.
Practical Applications of Automatic Machine Maintenance Monitoring
In the manufacturing industry, maintenance monitoring systems help businesses monitor the status of machinery such as production lines, automated robots, and heavy industrial equipment.
This system is applied in the maintenance of wind turbines, generators, and solar power systems, ensuring stable and continuous operation.
Monitoring devices are used to monitor the condition of engines, wheels, and braking systems on vehicles such as trucks, trains, and airplanes.
Maintenance monitoring helps maintain stable operation for medical equipment such as X-ray machines, MRI machines, ensuring accuracy and safety in treatment.
Application of maintenance monitoring in water systems, waste treatment, and urban infrastructure systems to increase operational and maintenance efficiency.
Automatic machine maintenance monitoring is not only a trend but also an optimal solution to help businesses improve production efficiency, reduce costs, and ensure stable operation of machinery. With the development of technology, the application of this system is becoming easier and more essential in every field.