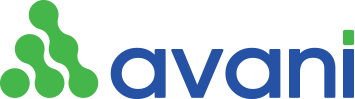
So, what is an automated maintenance system and why is it so important?
An automated maintenance system is a comprehensive management software that helps digitize and automate maintenance activities in the factory. It not only helps track maintenance schedules but also predicts potential incidents, thereby minimizing downtime and extending the lifespan of equipment.
Here are 5 key benefits that an automated maintenance system brings to your factory:
1. Automated Maintenance Scheduling: Instead of manual management with paperwork or spreadsheets, the system automatically creates and manages periodic maintenance schedules for each device. Schedules are established based on usage frequency, manufacturer recommendations, or other technical parameters. This helps ensure that all equipment is maintained on time, minimizing the risk of unexpected failures.
* SEO Optimization: Periodic maintenance schedule, automated maintenance schedule management.
2. Early Failure Warning, Minimize Downtime: The system collects and analyzes data from sensors and IoT devices to detect anomalies. Upon detecting a risk of failure, the system sends alerts to technicians, allowing them to intervene in a timely manner before an incident occurs. This helps minimize downtime and save on repair costs.
* SEO Optimization: Failure prediction, incident warning, downtime reduction, preventive maintenance.
3. Integrated Mobile Maintenance Process: Technicians can access maintenance information, work schedules, and incident reports directly on their mobile phones or tablets. This helps them work more efficiently, especially when moving around the factory. Recording and reporting work also becomes faster and more accurate.
* SEO Optimization: Mobile maintenance app, maintenance on phone, mobile maintenance software.
4. Efficient Management of Supplies and Spare Parts: The system helps track the quantity and location of supplies and spare parts in the warehouse. When needed, the system will automatically create purchase requests, ensuring that there are always enough supplies to serve maintenance work. This helps minimize material shortages and delays.
* SEO Optimization: Inventory management, spare parts management, maintenance supplies management.
5. Effective Reporting and Analysis: The system provides detailed reports on maintenance costs, equipment performance, and failure frequency. Based on these reports, managers can make informed decisions to improve maintenance processes and optimize costs.
Conclusion:
Implementing an automated maintenance system is a smart investment for any factory in Vietnam. It not only helps improve operational efficiency but also reduces costs, enhances competitiveness, and ensures sustainable development in the future. Contact us today for advice and deployment of an automated maintenance system tailored to your needs!