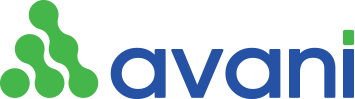
The Andon system is a tool for monitor manufacturing status that Toyota has applied to visualize problems to thoroughly solve it. The system is also a tool to speed up the production process to ensure progress and quality in production.
When a problem occurs, the andon system will immediately notify the related departments to focus on solving the problem, and stop manufacturing line. Departments from Technical, Team leader to Maintenance, Materials, Quality, etc are all responsible for their related items. Whenever the line is there and must stop for some reasons / incidents, the relevant department is responsible for approaching and solving the problem immediately. The problem is solved early, the stop duration will shorten, improve productivity and progress. The problems that are solved early also help to reduce faulty semi-products through the next stages from which the defective products are formed. As such, the andon system promotes improved production efficiency, including three factors: Availability, , Performance and Quality.
The Andon system will include pull cords or buttons at the workstations. Events informed by workers will be notified on the Andon system through the tools: Signal lights, sounds, monitoring screens at plant and related departments. The andon system also records the whole incident logs, calculates response times, responds to incidents to form a report for consideration of improving production efficiency.
With experience in consulting, manufacturing and supplying andon systems for many large factories, and applying Industrial Internet of Things, Avani will give your factory an optimal solution, effective, suitable with most appropriate quality, progress and investment costs.