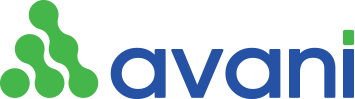
Real-Time Data: The Key to Predictive Maintenance
The core of applying IoT in maintenance lies in the ability to collect and analyze real-time data from devices and machinery. IoT sensors attached to equipment continuously record critical parameters such as temperature, vibration, pressure, energy consumption, etc. This data is transmitted to a central system for analysis.
Identifying Precise Maintenance Times
Instead of relying on periodic maintenance schedules (which often lead to premature or late maintenance), IoT systems allow businesses to implement predictive maintenance. By analyzing real-time data, the system can detect anomalies and warn of potential breakdowns. This allows businesses to plan maintenance precisely when needed, before problems occur.
Reducing Overall Maintenance Costs
The greatest benefit of IoT is its ability to reduce maintenance costs comprehensively:
* Reduced downtime: Predictive maintenance helps prevent unexpected failures, minimizing machinery downtime for repairs.
* Optimized use of spare parts: Instead of periodic replacements, only the parts that are actually needed are replaced, saving costs.
* Reduced labor costs: Diagnostics and repairs are performed more efficiently thanks to accurate information from the IoT system.
* Extended equipment lifespan: Timely maintenance helps prevent serious damage and extends the lifespan of equipment.
IoT Applications in Maintenance: Prospects in Vietnam
In Vietnam, the application of IoT in maintenance is becoming increasingly popular, especially in manufacturing, energy, transportation, etc. Businesses are realizing that investing in an IoT system is a smart investment, yielding long-term returns.
Conclusion
IoT systems are not just a new technology but also a strategic solution that helps businesses optimize maintenance planning, reduce costs, increase operational efficiency, and enhance competitiveness in the market. If you are looking for a solution to improve your maintenance operations, consider applying IoT today.