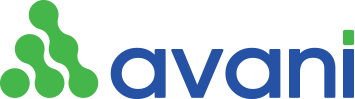
The cost of installing a monitoring system (sensors, CMMS software, IoT) often requires a large budget.
Many businesses are hesitant to invest because it is difficult to predict specific benefits in the short term.
Make a detailed financial plan: Clearly define ROI (Return on Investment) through reducing unexpected repair costs and increasing equipment efficiency.
Apply step by step: Start with important equipment with high risk of failure, then gradually expand.
Proactive maintenance technology requires engineers and operators to understand data analytics, use IoT technology and advanced software.
Traditional engineering teams are not properly trained in this field.
Internal training: Organize practical courses and update technology regularly.
Attract talent: Develop a policy to recruit and retain experienced engineers.
Collaborate with experts: Seek out partners with expertise to support implementation and initial training.
Challenges and solutions of proactive maintenance in manufacturing
Managers and employees are often accustomed to reactive or preventive maintenance methods, making it difficult for them to accept the transition to proactive maintenance.
Misconceptions that maintenance is only necessary when equipment fails.
Internal communication: Emphasize the long-term benefits of proactive maintenance, especially cost reduction and productivity gains.
Improve workflow: Incorporate proactive maintenance into production planning, avoiding disruption to existing operations.
Demonstrate effectiveness: Use real-world data to demonstrate improvements after implementation.
Many businesses use legacy equipment that lacks IoT or sensor connectivity.
Integrating a new maintenance system with existing processes can be complex.
Upgrade equipment piecemeal: Prioritize critical equipment or machines that require a lot of monitoring.
Use middleware: Apply solutions like retrofit to retrofit older equipment with sensors.
Participate with vendors: Work with partners who have experience integrating new systems with existing platforms.
Historical equipment data is not recorded or managed well.
Data collection system is not synchronized or inaccurate.
Build a database: Centralize the digitization of equipment maintenance and operation records.
Use CMMS software: Help store, analyze and manage data effectively.
Start with real-time monitoring: Collect data from modern sensors to replace outdated information sources.
Proactive maintenance technology is constantly evolving, requiring businesses to update and improve the system regularly.
Follow trends: Send teams to seminars and events on maintenance technology.
Flexible investment: Choose technology solutions that are scalable and integrated in the future.
Partner with service providers: Get partners to support system upgrades and maintenance. Implementing proactive maintenance is a process that requires a large investment in terms of finance, human resources and management thinking. However, with a specific plan, support from technology and commitment from the leadership, businesses can overcome these challenges to achieve higher production efficiency and minimize operational risks.