Automated Machine Monitoring (Automated Machine Monitoring) is the process of using technology to monitor the operation of machinery in a manufacturing or industrial process. The main goal of computer monitoring is to improve the performance, reliability, and overall system.
Key elements of Automatic Machine Monitoring:
- Sensors: Use sensors to collect data about the status of the machine, considering things like temperature, pressure, vibration, and energy consumption.
- Data acquisition system: Data from sensory sensors is collected and transmitted to a central system for processing and analysis.
- Data analysis: Use algorithms and software to analyze data, detect potential problems, and predict when maintenance is needed.
- User interface: Provide information to users through dashboards and reports, making it easy for managers to monitor the status of machinery.
- Integration: Connect with other systems such as ERP (Enterprise Resource Planning) to optimize production processes.
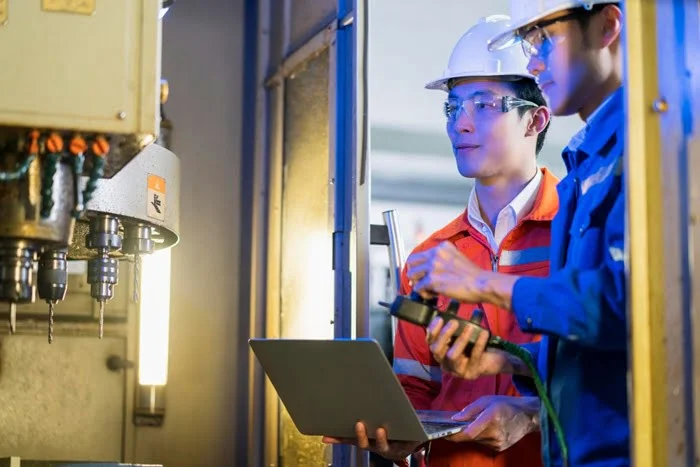
Benefits of Automatic Machine Monitoring:
- Increase efficiency: Support to optimize machine operations, reduce machine downtime.
- Reduce maintenance costs: Maintain predictability, maintenance can be performed before machine failure, saving costs.
- Improve product quality: Continuous monitoring helps to detect errors early in the production process.
- Enhance safety: Develop and warn responses to dangerous problems.
Automatic machine monitoring is becoming increasingly important in modern industries, contributing to the optimization of production processes and improving economic efficiency.