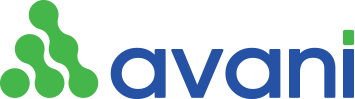
In industrial production today, a lot of machinery is applied automation in high levels. Those machines operate independently with their high automatic features. So how we can centralized monitoring of all machinery and other support devices be done continuously or just in time?
In many factories, the monitoring operation status of machinery is presented in the white board and is updated manually – called Machine Running Information. The information panel shows a list of machines and next to them are colored labels showing their operating status (Running / Stopping / Maintenance / Change Model…). Manufacturing teams will have to constantly update the status by changing the labels for each machine.
Andon system – with slogan “displaying information about the manufacturing status visually at sight” will be an effective solution for this situation. The sensors will be mounted to machines for listening working status, updating information to the central system to help instantly update the automatic monitoring electric board. Also monitor the actual operating time of the machine is accurately, easily calculate indicators of performance, operating productivity and equipment exploitation.
At the simple level, the system “Operation Monitoring of Machinery” only monitoring the running / stopped status of the machine, shows instant information and calculates performance based on running duration and running plan. At the advanced level, the sensors will connect more deeply to the controller (PLC), recording detailed information about the machine speed, the product model is manufacturing, the actual product completed, the specific error status if any … Then system can calculate Running time, Running productivity and Product quality, easily calculate OEE indicator – overall equipment efficiency quickly, accurately and completely automatically. . The OEE indicator is considered to be the measure of the effectiveness of the most important industrial manufacturing.
Andon system is unique in that it only GETs information, so connecting to machines at any level does not affect the control system and operation of the machine. Andon sensor devices are “Read Only” allowable parameters without any action affecting those values, so the system is always guaranteed to operate and data safety
With the development of connectivity technology, the Andon system enables the implementation of many effective wireless connectivity solutions in industrial environments such as: Radio Waves, Zigbee Technology or Bluetooth…, help installation time is shorter, improve effective maintenance warranties, do not affect the plant’s existing infrastructure and communications.
Wireless Andon systems are the indispensable trend in the application of automation and the Industrial Revolution 4.0 in manufacturing with Industrial Internet of Things – IIoT.