Automated maintenance monitoring is a process that uses technology and automated systems to monitor and control the condition of equipment and machinery in manufacturing facilities or engineering structures. The goal of an automated maintenance monitoring system is to detect early signs of failure or performance degradation so that timely maintenance can be performed, unexpected incidents can be minimized, and system operations can be optimized.
Main components of an automated maintenance monitoring system:
- Monitoring sensors: Installed on equipment to monitor parameters such as temperature, vibration, pressure, sound, humidity, and many other factors.
- Data storage and analysis system: Collects data from sensors and stores them for analysis. Modern systems often use artificial intelligence and big data analysis to predict equipment conditions.
- Maintenance management software: Integrate data from the system to manage maintenance schedules, helping engineers and maintenance staff grasp the status of equipment.
- Automatic notification: When a problem is detected or when equipment needs maintenance, the system will send a warning to employees via many forms such as email, text messages or management applications.
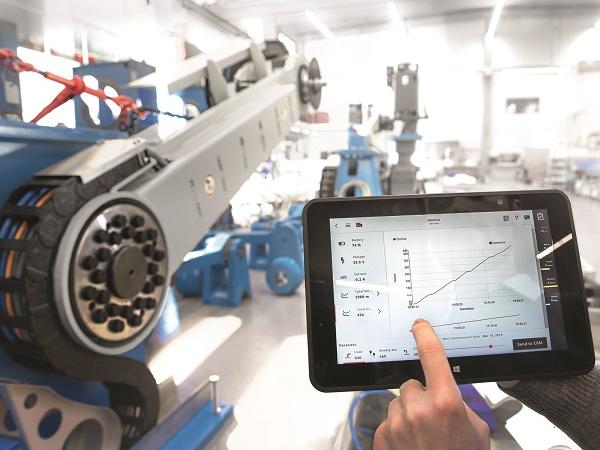
Automated Maintenance Monitoring System
Benefits of automatic maintenance monitoring
- Increase equipment life: Thanks to early detection of problems, repairs and maintenance can be performed promptly, avoiding serious damage.
- Reduce maintenance costs: Limiting serious incidents and optimizing maintenance time will help save costs.
- Improve efficiency: Stable equipment will help the production process run smoothly, limiting interruptions.
- Labor safety: Minimize dangerous situations for workers when equipment is unexpectedly damaged.
Automated maintenance monitoring applications are becoming increasingly popular in industrial sectors such as manufacturing, energy, transportation, and construction, thanks to the development of IoT, big data, and AI technologies.