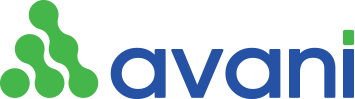
Smart manufacturing is simply understood as making the machinery system, support components and equipment become smarter, able to “communicate” with people to inform all current operating conditions, handle the situations under established procedures, improve operational efficiency, minimize downtime, waste, and ensure improved productivity and quality.
The Digital transformation in manufacturing is described in 5 stages:
IIoT – Industrial Internet of Things is a basic step that helps businesses realize 4/5 stages in the above process.
In order to do that, the machines and equipment will be equipped with sensors with many different features and be connected to each other through the appropriate network environment in each factory.
With the created connection, machinery and equipment “notify” all parameters, status of machines, software systems help simulate the operation process, help the operators to monitor and control the data continuously real-time
Detailed and continuous operational data is collected to form a valuable information warehouse, which helps analyze and detect wasteful points, bottlenecks make operational efficiency reduced, then find solutions to optimize and improve (Kaizen) .
Along with the above analysis, the departments will develop / improve operating procedures, provide basic automation scenarios, in order to make the system of machinery and equipment able to perform tasks automatically through connection.
The data warehouse collected will be the premise to proceed to stage 5: apply Artificial Intelligence to operate smartly, improve automation, minimize the impact of operators in complex scenarios, predictive problems and response immediately.
iAndon solution – a complete upgrade for the traditional Andon system with 4.0 technology is the IIoT solution, helping factories gradually overcome the stages to complete the digital transformation process, towards smart manufacturing with powerfully and comprehensive.