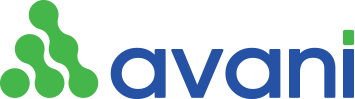
One of the biggest advantages of using IoT in machinery monitoring is the ability to continuously collect data from sensors and connected devices. Sensors can monitor many parameters such as temperature, pressure, rotation speed, and other parameters related to machine operation. This data is transmitted to information management systems, allowing staff to track and analyze data effectively.
Monitoring through IoT helps predict problems and prevent them before they happen. By monitoring operational metrics, the system can detect potential problems or performance declines early, allowing staff to take corrective action before serious machine problems occur. This helps minimize downtime and repair costs.
Besides, using IoT helps optimize maintenance schedules. Based on actual operational data, management systems can determine the ideal interval to perform routine maintenance. This helps avoid unnecessary maintenance, reduces costs and increases the life of the machine.
Another strong point of IoT is the ability to interact and control remotely. Employees can monitor and control machinery from anywhere via mobile devices or personal computers. This provides flexibility and convenience in production management, especially when problems need to be resolved immediately without the need to be on site.
Finally, the use of IoT technology in machinery monitoring also brings transparency and transparency in the production process. Operational data is stored and available for inspection, helping to create a transparent tracking system. This not only increases the reputation of the business but also aids in compliance with industry standards and workplace safety requirements.
To summarize, applying IoT technology in monitoring machine operating indicators not only helps improve production efficiency but also opens up many opportunities to optimize production processes, predict problems, and Enhance transparency in industrial production management.