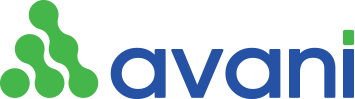
Main functions:
Maintenance schedule management: CMMS supports periodic maintenance planning, avoiding delays or omissions of important maintenance items.
Asset tracking: The system provides detailed information on the status, history and life of equipment.
Spare parts inventory management: CMMS helps track spare parts, ensuring that they are always available when needed.
Industrial Maintenance Management System: Concept and Effective Application
Improve equipment reliability and longevity: CMMS helps plan and perform maintenance at the right time, minimizing unexpected breakdowns and extending equipment life.
Reduce maintenance costs: Scheduling routine maintenance and predicting failures can significantly reduce emergency maintenance costs, minimizing major repair costs.
Optimize resources: CMMS helps allocate work appropriately to the maintenance team, avoiding overload or waste of human resources.
Improve productivity: By reducing equipment downtime and optimizing maintenance schedules, CMMS helps maintain continuous and efficient production operations.
Preventive Maintenance: This is a type of maintenance that is performed on a scheduled basis, to prevent potential problems. For example, checking and changing machine oil monthly or quarterly.
Predictive Maintenance: Based on real-time data, CMMS can analyze and predict when equipment will fail, thereby planning appropriate maintenance.
Corrective Maintenance: Performed when equipment has a problem, to fix and return the machine to normal operation.
Condition-based Maintenance: Performed based on the actual condition of the equipment, not on a predetermined schedule but based on actual indicators such as temperature, vibration or unusual noise.
Internet of Things (IoT): IoT sensors attached to equipment help monitor the condition of machinery in real time and send data to CMMS. This allows the system to detect abnormalities early and plan maintenance quickly.
Artificial Intelligence (AI) and Machine Learning: AI can analyze maintenance data to predict failure trends and recommend optimal maintenance schedules.
Cloud computing: Cloud-based CMMS makes it easy for businesses to access the system from anywhere and share data between related departments.
Mobile devices: Maintenance staff can use mobile applications to update work, check maintenance history, or receive notifications when problems need to be handled.
Assess needs: First, businesses need to determine their specific needs: the number of devices to manage, maintenance frequency, and available resources.
Choosing CMMS software: There are many CMMS solutions on the market with different features and costs. Businesses need to choose the solution that best suits their needs and scale.
Data collection and entry: All equipment information, maintenance history, and asset information must be entered into the system for the CMMS to function effectively.
Employee training: Ensure that all maintenance staff know how to use the CMMS, from data entry to tracking and reporting.
Monitoring and adjustment: After implementation, businesses need to monitor the effectiveness of the system and adjust processes to ensure the system operates optimally.
An industrial maintenance management system (CMMS) brings many important benefits to businesses, especially in optimizing maintenance processes and improving productivity. Implementing a suitable CMMS system helps businesses reduce costs, increase equipment reliability, and optimize maintenance resources.