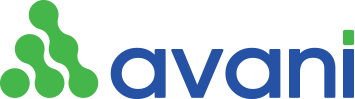
Failure prediction: Machine monitoring equipment provides continuous information about the operating status of machinery. Thanks to sensors and monitoring systems, managers can recognize precursor signs of impending problems. This helps them perform predictive maintenance, prevent breakdowns and minimize downtime.
Increase continuous operation: By monitoring operating parameters such as temperature, pressure, speed and vibration, machine running monitors help managers evaluate and maintain machine stability hook. Detecting and fixing technical problems promptly helps minimize machine downtime and increase the continuous operation of the production line.
Optimize maintenance processes: Data from machine monitoring devices provide reliable information to determine the right time for routine maintenance and component replacement. Instead of relying on fixed schedules, managers can determine the most optimal time to perform maintenance, minimizing disruptions in the production process.
Cost savings: By detecting technical problems early and performing proactive maintenance, businesses can avoid major breakdowns and unnecessary repair costs. At the same time, optimizing maintenance processes also helps reduce waste and save costs due to machine downtime.
Improve performance and reliability: By maintaining machinery equipment in the best operating condition, machine monitoring equipment helps improve the performance and reliability of production systems. This helps businesses maintain competition in the market and create trust for customers about product quality.
This is an important tool to help businesses maintain stable operations and improve performance in today’s production environment. Please contact Avani for advice on the most effective and economical solution!