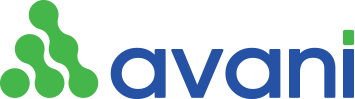
However, starting a smart factory is not an easy process. It requires thorough preparation and careful planning from the initial stages.
Below are some basic steps a business can consider as they begin their journey to transforming into a smart factory.
1. Assess current status and goals:
First of all, businesses need to evaluate the current status of the current production system to clearly understand the strengths and weaknesses. They then need to set specific goals for the transition to a smart factory, including performance, cost, quality and flexibility targets.
2. Identify suitable technology:
Based on the set goals, businesses need to identify the specific technologies they need to deploy to turn their factory into a smart manufacturing environment. This can include automation systems, IoT sensors, artificial intelligence, machine learning and blockchain, depending on the specific requirements of the business.
3. Human resource training:
Transforming into a smart factory requires not only investment in technology but also investment in human resources. Businesses need to ensure that their employees are trained and ready to work with new systems and technologies.
4. Develop an implementation plan:
The implementation plan needs to be carefully developed, including specific steps, time and required resources. This includes scheduling the implementation of each phase of the project and ensuring continuity of the transition process.
5. Test and adjust:
Once deployed, testing and tuning is an important step to ensure that the system operates effectively and meets its objectives. Businesses need to perform thorough checks and adjust processes as necessary to ensure project success.
Therefore, starting to build a smart factory requires careful preparation and careful planning from the initial stages. However, if done properly, this transformation can bring significant benefits to businesses, from increasing production efficiency to optimizing processes and minimizing costs.