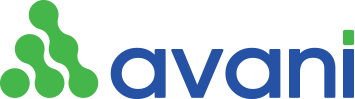
There are seven important indicators used on manufacturing as below:
An essential factory floor metric relates to the amount of product produced. The count (good or bad) typically refers to either the amount of product produced since the last machine changeover or the production sum for the entire shift or week. Many companies will compare individual worker and shift output to invoke a competitive spirit among employees.
2. Reject Ratio
Production processes occasionally produce scrap, which is measured in terms of reject ratio. Minimizing scrap helps organizations meet profitability goals so it is important to track whether or not the amount being produced is within tolerable limits.
3. Rate
Machines and processes produce goods at variable rates. When speeds differ, slow rates typically result in dropped profits while faster speeds affect quality control. This is why it is important for operating speeds to remain consistent.
4. Target
Many organizations display target values for output, rate and quality. This KPI helps motivate employees to meet specific performance targets.
5. Takt Time
Takt time is the amount of time, or cycle time, for the completion of a task. This could be the time it takes to produce a product, but it more likely relates to the cycle time of specific operations. By displaying this KPI, manufacturers can quickly determine where the constraints or bottlenecks are within a process.
6. Overall Equipment Effectiveness (OEE)
OEE is a metric that multiplies availability by performance and quality to determine resource utilization. Production managers want OEE values to increase because this indicates more efficient utilization of available personnel and machinery.
7. Downtime
Whether the result of a breakdown or simply a machine changeover, downtime is considered one of the most important KPI metrics to track. When machines are not operating, money isn’t being made so reducing downtime is an easy way to increase profitability. Organizations that track downtime typically require operators to enter a “reason code” via keypad, pushbutton or bar code scanner so that the most common reasons can be reviewed at a later time.
At Avani, we manufacture and supply andon solution packages – operation monitoring in manufacturing to help factories track key indicators through collecting status, information, analysis data, calculate real-time indicators, display in visual areas, support continuous monitoring to help detect factors that influence effectively, thereby improving processes, improving labor capacity to continuously increase labor productivity over time.