One of Toyota's lean (Lean) philosophy is eye management. The automated systems mean: if there is an abnormal production problem, machinery and equipment must be stopped. The key here is to make a clear distinction between what is normal and what is unusual. In terms of quality, it is the exposure of bad, defective products. In terms of quantity, it is how to see if production is on time or not on schedule. This is considered a simple and true way of thinking for all things. So eye management is done thoroughly by Toyota. The Andon system is a prime example.
In the beginning, Toyota used Andon light pole to hang each machine in the factory, the production line was operating in a normal state, the light was green. Assuming that the worker wants to get help from outside to adjust the work schedule (due to an error, due to delay ..), the orange light will be displayed. When it is necessary to stop the line to correct the error, the Andon signal will turn red. To eliminate the irregularities a line stop is necessary.
Science and technology have developed, Andon systems are moved from static Andon boards to real-time alerts on digital signage or TV screens, computers … Andon systems are a combination of:
- Large production area screen
- Use existing operating equipment and production area terminals
- Alert technology: email or SMS or combination
- Improve communication between operators and engineers, and operator workers
- Maximum display of warnings: indicator light image, sound …
- Improvement of OEE and quality (OEE is an index used to measure the overall performance of the equipment through all three aspects of resources, namely time, manpower and operating speed.)
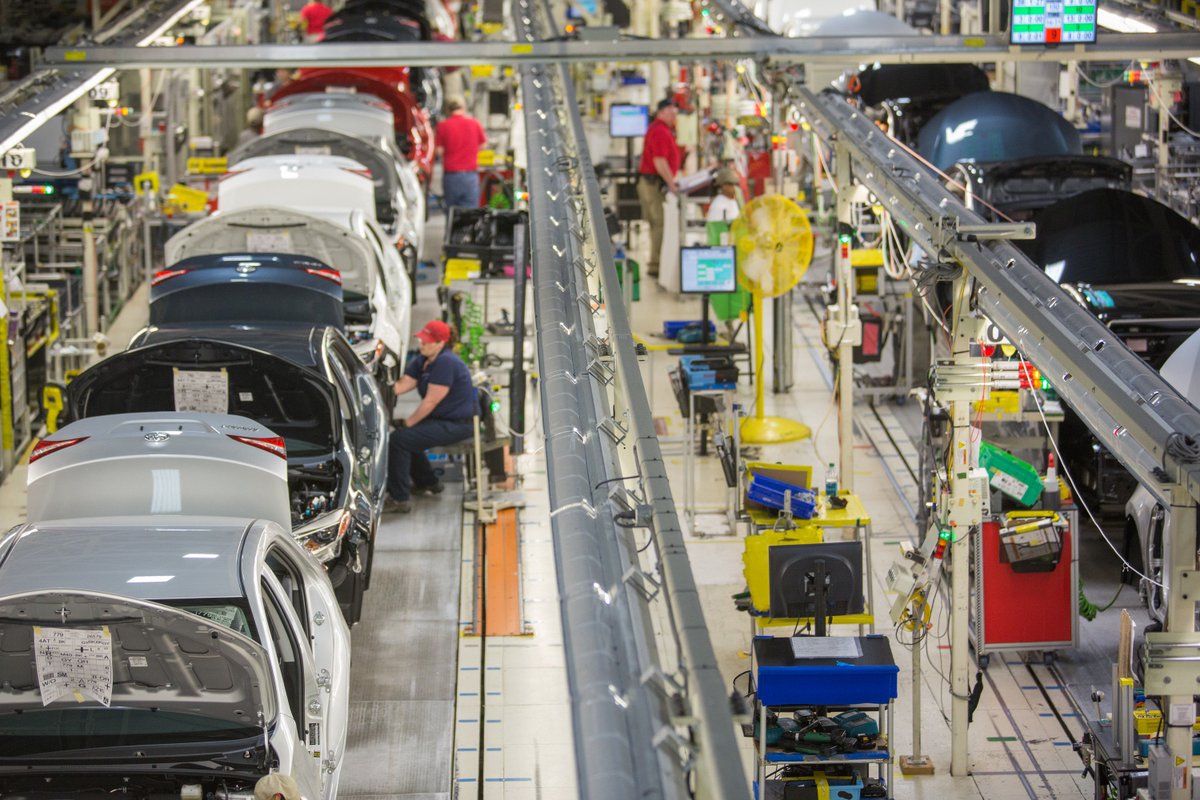
Andon systems in Toyota lean manufacturing
Using the Andon system in lean manufacturing has many benefits in the short and long term. In short, the system provides:
- Transparency in the production process of machinery, equipment and workers
- Increase labor productivity and production efficiency
- Minimize redundant products, errors …
In the long run, the system helps:
- Reduce costs and downtime of machinery and equipment.
- Improve product quality, improve competitiveness for businesses
- The executive managers have an overview of the production and business activities, and promptly adjust if there is an abnormality.
- Improve the operational efficiency of the production process.
Like most principles of Lean manufacturing, the Andon System itself has no value without understanding and properly applied it. When used for the right purposes, the system will bring about great effects, improve profits and increase competitiveness of businesses.