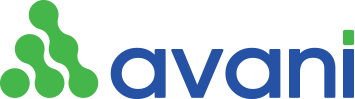
In the mechanical industry, the application of automatic monitoring of machine system indicators in manufacturing plants is not only a requirement but also a decisive factor to ensure performance, accuracy and efficiency. safety during production. Automatic monitoring systems in the mechanical industry play an important role in maintaining and improving product quality.
One of the main applications of automatic monitoring in the mechanical industry is monitoring the operating indicators of machines, machine tools and production equipment. Sensors can continuously measure pressure, temperature, rotation speed and other parameters, helping factory managers monitor the performance of equipment. If there are any problems or performance drops, the system will alert immediately, helping management staff take timely corrective measures.
Automatic monitoring systems also play an important role in ensuring labor safety. By monitoring safety-related parameters such as pressure, temperature, and machine operation, the factory can issue warnings when there are incidents that may affect labor safety. This presents an opportunity to prevent accidents and minimize risks to employees.
Automatic monitoring also assists in managing productivity and saving energy in the mechanical industry. By monitoring machine and equipment productivity, factories can optimize production schedules and reduce the risk of bottlenecks. At the same time, the system can also detect and recommend energy saving measures, helping the mechanical industry move towards sustainability and saving resources.
The application of automatic monitoring of machine system indicators in the mechanical industry brings many benefits, from enhancing production efficiency to ensuring labor safety and saving energy, contributing to development. and sustainability of the modern mechanical industry.