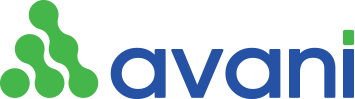
Lean Manufacturing – lean manufacturing originated and has been implemented throughout Toyota factory operations since the 1950s. Up to now, Toyota has always been considered as one of the companies applying Lean Manufacturing most effectively.
The role of MES in Lean Manufacturing
The purpose of Lean Manufacturing is to identify and eliminate all types of waste – all related wastes, work that does not bring value to customers and production, calculate excess removal of input materials that cause redundancy, limited defective products, recycling costs and other features that are not in the needs of the customer.
MES is a system that provides real-time production monitoring solutions. Enables managers to capture, provide, and track the data needed for production operations in the most efficient manner and most appropriate execution.
For Lean Manufacturing to be effective, it must follow the expected real-time measurement and tracking, and at the same time have the analysis and control of those corresponding real-time production data. The data collection conducted by MES will increase efficiency and quickly help manufacturers solve problems quickly. MES will approach Lean by supporting and reinforcing correct practices, measuring operational performance and improving production processes, eliminating waste. MES will ensure the success of innovative methods in lean manufacturing.
In addition, MES will support the implementation of various steps in the lean manufacturing process such as calculating and tracking OEE, 5S methods, etc. Thus, MES plays an important role in Lean Manufacturing, businesses should consider to use to fulfill their production purposes most effectively.