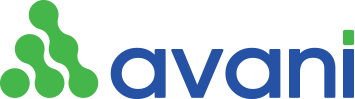
Previously the Andon system was used as a production warning system, warning parts such as engineering, direct production staff … about an abnormal change in the production line, from there. Support department quickly access to information processing and return production activities to normal state.
The Andon system’s general operating principles are to detect problems, generate sound / video of fault warning and troubleshoot, bring production back to normal state.
The Andon system was born and applied before World War II, bringing many effects to the manufacturer, mainly Toyota. At that time, the Andon system operated simply: Human detects the problem, then pushes the button / pulls the cord; Indicates whether the problem is a light panel or an alarm. After the troubleshoot is completed, the button / pull of the line is pressed again to notify the production line back to the normal production state.
Revolution 4.0 is a revolution that has been taking place strongly in the world as well as in Vietnam. In fact, all new technologies are not applied at the manufacturing factories, but are prioritized according to the order of management needs and production practices. Therefore, factories planning to apply the success of technology to production must always evaluate – consider benefits and costs before starting to deploy.
The Andon system in the Industrial 4.0 era
In the era of science and technology 4.0, besides traditional devices such as buttons, switches, zippers, lights, bells, today’s Andon system incorporates the use of more modern equipment. At fault detection, the system may be equipped with sensors, cameras, or production metering equipment. The parameters are then evaluated by the comparison software program against the given conditions to generate the alarm signals.
The Andon system can display the problem through devices such as TV screens, computers or send emails, send text messages or call the responsible supervisor and related department. Here, the Andon system is set up not only to notify one person once, but also to forward notifications to others if after a certain period of time no one confirms or responds.
Since the new notification devices are used, when the troubleshooting is completed, the assistant can confirm on the touchscreen display or simply speak into the voice command microphone. The system will automatically record and announce on the screens showing the normal production status.
Andon system management software can integrate data with other production management software currently in the factory.
The most important difference between the new Andon systems today is manageability and interoperability.
When the production alarm system is traditionally stopped at a level of independent operation, and mainly informing field personnel. When you want to store details of the arising incidents (when the incident occurred, the time of processing, the person to handle …), people need to manually record the information in the book. This approach was appropriate in the past when the factory had fewer machines and less production needs. In the 4.0 era, the Andon system uses management software that allows managers to review real-time incident history as a visual chart whether at or not at the factory.
Andon system also integrates data with other computer software such as production management system MES, energy management system PMS or maintenance management systems of production equipment. For example, in a month or a period, a device is constantly failing, data on the number of failures occurred with that device is transferred to the equipment maintenance management software, from which the manager has a plan. replace and maintain the equipment in order to limit the problem of the machine from continuing. Or when the raw materials are finished production each time, the production management systems automatically subtract the remaining materials in stock to more accurately reset the production scheduling process, reducing shortages. or redundant.
Thus, the Andon system – the production warning system, has been changing in response to the requirements of industrial revolution 4.0 production. The role of the Andon system remains very important in many manufacturing plants. Therefore, if your company is in need of a solution to improve production quality, please find out and contact us to have a suitable Andon system.