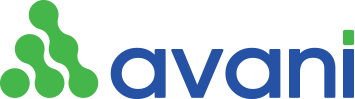
The operation of the Andon system includes the following steps:
1. Continuous monitoring
Andon works by continuously monitoring the status of the production line. It can be integrated with sensors, machines and automation systems to detect problems in the production process.
Workers on the line can also proactively activate Andon (if allowed) when they detect errors or need help in their work process.
2. Warning
When an incident occurs (e.g. machine failure, product quality failure, shortage of raw materials…), the Andon system will be activated.
Typically, warnings are indicated by lights (usually three colors or more depending on the specific production):
Green light: The system is operating normally.
Yellow light: Warning that a check or attention is needed.
Red light: Serious incident requiring immediate production stop and intervention.
Sound is played on the speaker system, electronic board (later TV screen) can also be used to widely announce to the entire factory.
3. Notification and communication
When Andon is activated, information about the incident will be immediately transmitted to the relevant departments.
It is possible to optionally send messages, make phone calls or use applications on smartphones, tablets of relevant personnel, helping them to intervene quickly.
Detailed information about the incident, the location of the incident will be clearly displayed, helping to analyze, approach and handle quickly.
4. Stop production (if necessary)
In many cases, if the incident is serious (such as a broken machine or a product with a major defect), Andon will stop the production line to avoid creating more defective products or causing damage to the machinery system.
Stopping production immediately saves repair costs and avoids mass production of defective products, saving time and resources.
5. Troubleshooting
When Andon is activated, a technical team or manager will go to the site to analyze and solve the problem.
Corrective actions may include repairing machinery, adjusting production processes, or retraining employees.
6. Continuous monitoring and improvement
Once the problem is solved, data related to the problem will be recorded and stored for later analysis.
The Lean system encourages continuous improvement (Kaizen), and data from Andon is a useful tool for understanding the root causes of problems and suggesting improvements to prevent recurrence.
This activity not only helps optimize the production process, but also improves product quality and increases line efficiency.
7. Encourage worker participation
One of the core principles of Lean is to encourage the active participation of all workers in process improvement.
Workers on the production line are encouraged to activate the Andon system when they detect problems, which helps to increase accountability, create a highly collaborative work environment, and quickly resolve problems, preventing problems before they become serious.
Andon in Lean Manufacturing is not just a tool, but also an important part of a culture of continuous improvement, encouraging employee participation, and helping to prevent problems. By providing real-time alerts and facilitating rapid intervention, Andon helps to increase production efficiency and reduce waste, thereby achieving the goal of the Lean model: providing high-quality products at the lowest cost and in the shortest time.