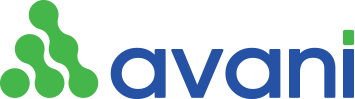
In the increasingly competitive environment with the global integration trend, with Third rank of export value in the World, to keep rank and possibly grow stronger, Vietnamese garment enterprises face with pressure on ensuring productivity, progress and product quality. Many garment companies around the world have adopted technology to help control and increase productivity. It is also a trend that Vietnamese businesses must follow.
In manufacturing, product counting and progress control are important. The garment products are not the shape of the block, so apply of automatic counting is relatively difficult. With the block products (such as tire, shoes, water heater, …), when the product passing through can use fit sensors to count automatically. For garment products, checkpoints are still required by workers to perform manual counting with the help of counters.
Our solution we proposed is to connect the counters at the lines, synchronize information throughout the factory for monitoring, tracking continuous and real time. This solution also saves labor when counting and quality control is concentrated at QC.
How does this solution work?
The solution have been successful and effective application in some FDI factories in Binh Duong, Phu Tho.
In addition, for more professional and accurate control, factories can apply Bar code and Radio Frequency identification technology. The application of these modern technologies will increase the cost of products as each product, because we have to add printing bar codes or chips to the product. Therefore, these forms are usually only applicable to premium segment products.
Applying modern technology, however, must be appropriate and flexible, which is the standard for all economic sectors, especially the manufacturing sector, towards a “smart manufacturing”.