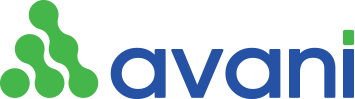
Andon is introduced by Toyota, which is part of Jidoka’s quality-control method and today is an essential part of Lean Manufacturing. Andon operates on a defined accelerate process with the information flow related to slowdowns and stops of the production system, and it has input/output components.
For input activation, first the pull cord system is most used, also known as Andon rope. The cord is hung on the ceiling, on hight can be reached by workers. Then, the pull cord system is replaced by buttons, because operation points and stops are fixed. More advanced is to use sensors (optics, magnetism, temperature …) to automatically detect defined problems or events.
For the output system, there will be output types: signal light display at event locations, audio system playing defined ringtones and screen display (Andon board ). Andon board in the beginning used a light box – the panel was lined up, each cell contained light bulbs of different colors. When activating an event at a certain location, the corresponding position on the light box will light up a light bulb and show it. This method is easy to deploy with existing equipment, but the deployment is quite complicated, too many wired, there are risks and difficult maintenance. In addition, the light box only display fixed information.
LED panel is next generation of Andon board. This table displays more flexibility by displaying multiple numbers at one location. However, the general layout is also limited. The most optimal option is to use the display on TV screen and controlled by software. This option allows to flexibly change the layout, information … according to each size, as well as use for other announcements. Today, with Smart TV, we are possible to build andon applications in web form, and Smart TV is used as a PC, exploiting applications via web browser (Web Browser).
About technology, the early Andon system mostly uses PLC programming unit. These sets will be added with extension modules (IO Extension) to connect multiple points through the signal wiring. The PLC set is programmed and connected to a computer set with communication software for reading information. This method solves the problems of the Andon system, however the cost for PLCs and expansion modules is relatively high. In addition, each line or a small area must have at least 01 PC to run the software.
Today, the Andon solution has been specialized with remote terminal equipment, connected via wires or wireless (Wifi, Zigbee). Andon software is also deployed on centralized servers, PCs or TVs can direct connect to the server without displaying a separate computer. This technology solution makes the connection flexible, easy to operate, maintain, and has a better price.
With the huge development of technology, the Andon solution is also upgraded and optimally optimized to better meet better requirements, fit new technology, improve connectivity and integration, improve effectiveness for manufacturing.