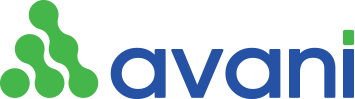
Day by day, pull cords have been replaced by buttons, communication using signal cables has been replaced by wireless communication technology. That makes the deployment and use of andon become more effective, easy and quickly to deploy, shorten the time of production impact as well as ensure aesthetics, more effective in warranty and system maintenance.
iAndon Call system package includes buttons at worker’s position, accompanied by tower light or signal rotation light turn on. The number of buttons and the corresponding light tower floor depend on the specific contents to be notified, for example:
There may be problems that will cause manufacturing line stop immediately or move to the nearest location. The relevant action and interaction scenarios will be defined.
When workers press the button at the position, the corresponding light will flash and there may be a horn to increase the attractiveness. At the same time, the Andon screen will receive information to show the problem, the location occurring with large numbers and an visual color. From there, the relevant departments will approach and support the problem solving, minimize downtime due to problems, solve early and neatly the problems that may cause failures for subsequent stages.
The Andon software system also records the problem log, the call start time, the response time and the finish time of the problem, forming a detailed log system, which helps to evaluate and analyze to improve production activities, improve efficiency, quality, enhance interactivity and continually update, as soon as any stage is needed without wasting resources waiting (just in time)
Avani is a professional iAndon supplier, with experience in deployment and technological capability, we will help the factory solve andon system-related problems, automate production monitoring to build a system with detailed information and multi-dimensional, towards smarter and more efficient production activities.