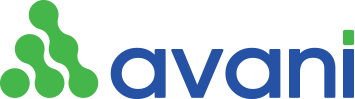
As we known, Andon is an inseparable component of lean manufacturing, but we need to understand more deeply that: it is closely related to the Toyota’s culture of face to failure. So at Toyota, Andon is applied and used like?
Andon is a system that displays production status on the lines, supported by buttons or pull cord, so workers can call help and stop the line if something goes wrong. After the problem is handled (by Line Leader or related departments such as Maintenance or Quality), the line resumes operation. At this point, everything is not over, because Toyota’s way is to solve the root causes, not only solve them. Therefore, a series of issues are posed: What causes the problem? How can we prevent it from happening again? Do we need a change or adjustment in the tools? Do we need a design change? Do we need to update working standards?
Because of the way they find and solve the root cause, they have created great efficency: In the beginning of production, the stopping time is quite large, even the downtime is longer than the running time, but only After a few months, the performance indicators will reach almost the “legendary” level, from 80-95%.
With such clear efficiency, many factories have invested in modern, expensive and luxury Andon systems. However, stopping the line clearly had an immediate effect. For many factories, stopping production means that we will lose money. Although stopping and resolving immediately will help prevent problems later, the mental factors make them not want to stop passing. When workers stop passing, they can be fined; The Line with many stopped time will be rated the lower efficiency. It gradually becomes a habit of “ignore the error,” if something goes wrong, it’s easy to push it to the next stage, and then it can lead to much bigger consequences. As such, investing in an expensive Andon system has not worked, because the Andon system itself is inefficient if the workflow system does not apply properly to it.
The value of the Andon system is its ability to use it. So need to change the workflow to make the most of its effectiveness. The system is always the body only, the soul is the information of human interaction to help the system collect. The establishment of a complete and measurable information system helps quantify factors, thereby improving production to improve efficiency continuously and sustainably.
Please contact us, we will help factories to advise Andon solutions appropriately and effectively, as well as assist in optimizing work processes to increase production efficiency, accelerate the process of factory digitization as well as work towards Smart factory in the near future.