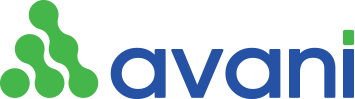
In the modern industrial manufacturing environment, monitoring automatic operating indicators in the factory plays an important role to ensure performance and safety. Automated monitoring systems not only help improve productivity but also minimize risks and reduce maintenance costs.
One of the important applications of automatic monitoring is to monitor and analyze the operating parameters of machinery and equipment in the factory. Sensors and automated systems can continuously measure parameters such as operating indicators, current consumption, environmental data and other relevant parameters. This data is then transferred to the monitoring system for analysis and results on operating performance as well as warnings in case of abnormalities.
The automatic monitoring system also helps monitor product quality. By continuously monitoring key parameters during production, factories can detect early on any issues that could affect product quality. This helps reduce waste and enhance product reputation.
In addition, automatic monitoring also plays an important role in energy management. The system can monitor the energy usage of devices and suggest energy saving measures. This not only helps reduce costs but also accelerates the transition to clean energy sources.
By automating monitoring processes, factories can optimize operations and minimize the risk of incidents. The early warning system helps management staff intervene promptly, thereby minimizing production interruptions and increasing efficiency.
The application of automatic monitoring of operating indicators in manufacturing plants not only brings benefits in terms of productivity and product quality, but also reduces risks and maintenance costs, while contributing to active participation. Participate in the sustainability of industrial production processes.