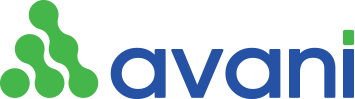
The Andon board shows issues, incidents or problems cause manufacturing disruptions, and also shows production plan, target and actual output to monitor and speed up the manufacturing process.
A component that can be considered at the core of Andon is the incident notification system, also called they are manufacturing failures based on Toyota’s philosophy. When occur any abnormal stuation, the worker will pull the wire or press the button at his position to active the Andon light, the buzzer and the Andon board shows notify, and also stops the manufacturing line.
When Andon announces the problem, the related departments will gather to solve the problem, reduce downtime and thoroughly solve the problem that caused the problem. The worker who reports the incident and stops manufacturing line will not be prosecuted for liability or be punished. The staff will confirm and report the relevant facts such as the activities order, how the incident arises … Then just wait for the relevant departments to solve the problem and turn the manufacturing line back into operation. . The culture of “Stop – Call – Wait” has been deeply rooted in the minds of every person at Toyota.
The key point is not to punish the worker who reported the incident and stop manufacturing line. Opposite, the person who reported the incident on the andon system was also said by people around them “Thank you for reporting the incident to Andon,” which is Toyota’s culture.
If reporting an andon incident is punished by the superior, then of course when there’s an abnormal problem, the Operator will want to hide it with the thought: “This bug probably doesn’t matter”, “Probably nobody will found out ”and continued to the next stage, the result would be a much bigger problem.
Toyota’s secret to bringing concealed failures out is not to investigate litigants, but focus on finding the root cause of the problem. That is the great benefit that Andon system brings to production.