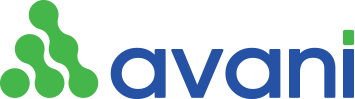
OEE (Overall Equipment Effectiveness) is an index to measure the overall efficiency and utilization of equipment as planned. This index helps managers and operators to find the index is not good, the point “dead” affects the efficiency to gradually improve and optimize.
OEE is made up of three indicators: availability, performance and quality. From these 3 indicators, we can easily identify the causes, factors affecting each indicator, the problems causing waste in the production cycle to improve step by step.
OEE calculations exclude scheduled downtime periods such as routine maintenance, mid-shift breaks, holidays or no orders. Based on this plan time, if the factory maintains the ideal production level: the production rate is right with the plan and the design capacity of the equipment, the product is 100% quality and there is not any abnormal issue that stop or slow down the production process. Thus, the OEE will reach 100%, this is the ideal level, but this level is almost impossible to achieve. For manufacturing factory in the world, the OEE of the device rated as “excellent” is usually around 85%. On average, OEE is typically around 60%, which is considered “good”.
To improve OEE, it is necessary to identify the factors affecting each of the indicators A, P, Q.
Indicator A – Availability.
Index A is often related to problems of malfunctioning, stopping for unusual maintenance or unplanned production, leading to a stop to installation of information for new products … To improve this index, must first improve the maintenance efficiency factor. A poor maintenance officer can increase the maintenance time simply by following up on the incident, decreasing the operational capacity of the machinery. With the help of technology, sensors or monitoring devices can help to accurately detect equipment failures immediately with type of issue and location, assist in fast and efficient maintenance.
Index P – Performance
The inadequate and untimely supply of materials, accessories reduces the work capacity, along with the operating and maintenance elements that increase the cycle time, resulting in lower efficiency. Applying sensors to detect and call supplies or maintenance will immediately reduce the time interval, shortening the cycle time to improve performance.
Index Q – Quality.
With traditional production methods, the end of production shifts will summarize the quality index. Thus, if the quality index is low, then correcting, repairing or supplementing it will take more time and resources after. If monitoring systems are used to monitor the quality status, if they are over the safety threshold, they will immediately notify and warn the concerned units for consideration and immediate treatment, thereby updating the process to avoid the wrong manipulation, make the products then quality assurance. This ensures that quality is always monitored within the safe range without make the cycle time longer.
As can be seen, smart manufacturing applications, including the sensor system is connected, gather information for instant warning and processing, forming data warehouse for analysis to optimize for the next orders, build software for production planning … will help the factory to have information system synchronous, effective, instant management and save the delay time, improve production efficiency is clearly visible.
In today’s competitive and fast-growing economy, enterprises must always improve their “competitiveness”. Improving efficiency, which is vital to improving competitiveness, by adopting solutions to improve OEE indicator. Applying technology with basic, specific steps of smart manufacturing will help Enterprises enhance this index, enhance competitiveness, build valuable data warehouses that help analyze and make future plans with the highest optimization, availability for expand applications in industrial revolution 4.0 trending.